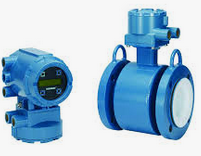
Magnetic flow meter calibration
The magnetic flow meter is a volumetric device used for electrically conductive liquids and slurries.
The magnetic flow meter design is based on Faraday’s law of magnetic induction, which states that:
"The voltage induced across a conductor as it moves at right angles through a magnetic field proportional to the velocity of that conductor." That is, if a wire is moving perpendicular to its length through a magnetic field, it will generate an electrical potential between its two ends.
Based on this principle, the magnetic flow meter generates a magnetic field perpendicular to the flow stream and measures the voltage produced the fluid passing through the meter. A set of electrodes detects the voltage.
The voltage produced is proportional to the average velocity of the volumetric flow rate of the conductive fluid.
The tube is constructed of non-magnetic material (to allow magnetic field penetration) and is lined with a suitable material to prevent short-circuiting of the generated voltage between the electrodes. The tube is used to support the coils and transmitter assembly.
Generally the electrodes are of stainless steel but other materials are also available. These electrodes have to be chosen with care to avoid corrosion.
Dirty liquids may foul the electrodes, and cleaning methods such as ultrasonic may be required.
Theoretically, it can measure flow down to zero, but in reality its operating velocity should less than 3 ft / s (1 m/s). A velocity of 6 to 9 ft/s (2 to 3 m/s) is preferred to minimise coating.
It should be noted that at velocities greater than 15 ft/s (5 m/s) accelerated liner wear could result.
This meter has no moving parts; and is unaffected by changes in
•Fluid
•Viscosity
•Pressure
Advantages
•Are bi-directional
•Have no flow obstruction
•Are easy to re-span
•Are available with DC or AC power
•It can measure pulsating and corrosive flow.
•It can measure multiphase; however, all components should be moving at the same speed; the meter can measure the speed of the most conductive component.
•It can install vertically or horizontally (the line must be full, however) and can be used with fluids with conductivity greater than 200 umhos/cm.
•Changes in conductivity value do not, affect the instrument performance.
Disadvantages
•It's above average cost
•It's large size
•Its need for a minimum electrical conductivity of 5 to 20 umhos / cm
•Its accuracy is affected by slurries containing magnetic solids (some meters can be provided with compensated output in this case).
•Electrical coating may cause calibration shifts
•The line must be full and have no air bubbles (air and gas bubbles entrained in the liquid will be metered as liquid, causing a measurement error).
•Vacuum beakers may require in some applications to prevent the collapse of the liner under certain process conditions
•In some applications, appropriate mechanical protection for the electrodes must be provided.
DC types are unaffected by variations fluid conductivity and thus are generally preferred. However, AC types are used for.
•Pulsating flow applications
•Flow with large amounts of entrained air
•Applications with spurious signals that may be generated from small
Electro-Chemical reactions
•Slurries with non-uniform particle size (they may clamp together)
•Slurries with solids not g well mixed into the liquid.
•Quick response.