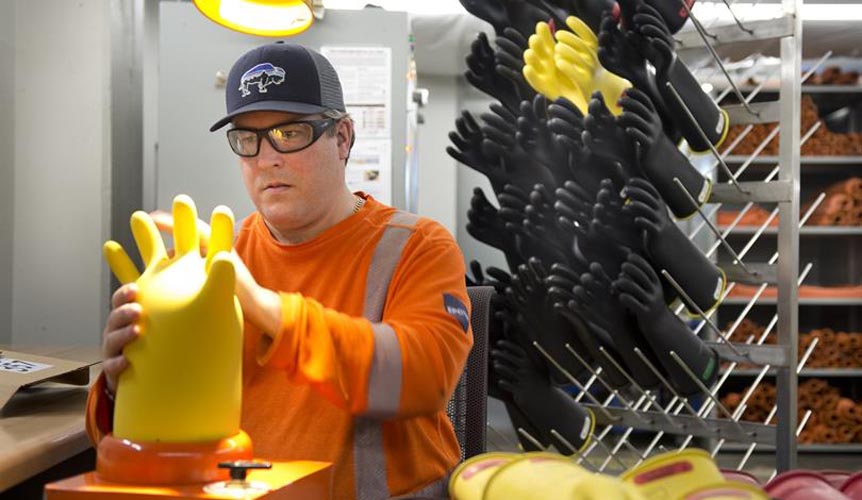
High voltage calibration UAE
High Voltage Testing Services
• Services are used by various organizations, including small electrical contractors, large electricity suppliers, and mining industries.
• Services include testing high voltage equipment, examining, cleaning, repairing, and stocking replacement components.
High Voltage Gloves
• High-voltage gloves are regulated by ASTM D120, NFPA 70E, and OSHA CFR 1910.13712.
• Regular checks are required before the first issue and every 6 months thereafter, or more frequently, such as once per month.
• Employees working on high-voltage surfaces may be subjected to higher voltage and more frequent testing.
Catering for the High Voltage Industry
• Calibration services are provided for various HV Industries including rail, power generation & distribution, electrical service & maintenance, and petro-chemical.
• Accredited by Megger, Seaward, and others.
• Calibration capabilities include discharge rods, high voltage sticks and indicators, flash testers, proving units, live line testers, and more.
Advantages of High Voltage Equipment Testing
• High quality and efficient testing services.
• Tests conducted by qualified power system electricians.
• Leading-edge high voltage test facility.
• Cleaning and repair of equipment.
• Testing for rubber insulated electrical gloves.
• Safety and maintenance tips for rubber insulated gloves.
Insulated Rubber or Plastic Cover-up Testing
• High voltage tests on a wide variety of rubber or plastic insulated cover-up equipment.
• Inspection and testing are crucial to ensure the electrical safety of the equipment.
• Electrical testing for compliance is governed by ASTM F478, ASTM F479, CSA Z462 (5.11.2 and 5.11.3), and ASTM F712 (plastic).
Fiberglass Hand-held Live-line Insulated Tool Testing
• Inspection, testing, and maintenance services for fiberglass hand-held live-line insulated tools.
• Electrical testing for compliance is governed by ASTM 711, ASTM 3121, and IEEE 978.
Protective Ground/Grounding Jumper Testing and Assembly
• Thorough mechanical, visual, and electrical testing for protective grounds, grounding cables, and bypass jumpers.
• Visual inspection of protective grounds/jumpers.
Insulated Boom Truck Testing
• Testing for bucket trucks and boom trucks.
• Visual inspection of the boom.
• Electrical testing for compliance is governed by CSA C225-10 and requires insulated booms to be tested at least every 12 months.