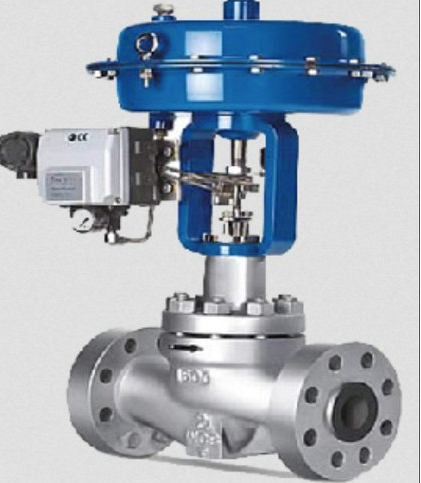
Final Control Elements/Control Valve
• Pneumatically actuated control valve is the final control element in process systems.
• It regulates fluid flow and provides power to translate controller's output to the process.
• Control valves consist of the actuator and valve body assembly.
• Types of control valves include sliding stem control valves, globe bodies, single port, double port, three-way, angle valves, and diaphragm valves.
• Globe valves provide tight shutoff, single port valves have high unbalanced forces, double port valves balance forces, three-way valves blend or divert streams, and angle valves can handle sludge and erosive materials.
• Diaphragm valves, also known as Saunders-Type valves, are suited for slurries and viscous fluids, have high capacity, and are relatively low in cost.