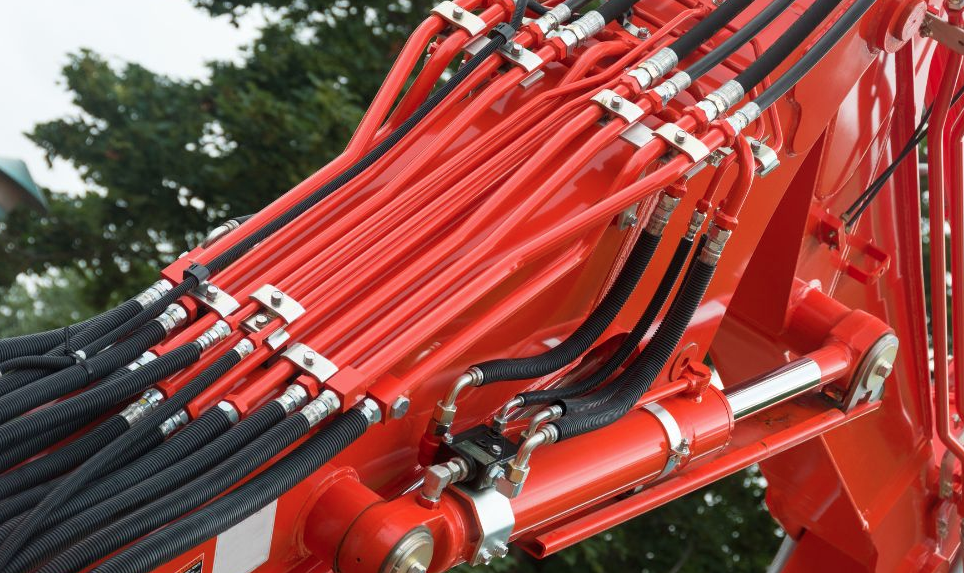
Why Hydrostatic Pressure Testing Is Important
Hydrostatic pressure testing is a process of pushing a pressurized vessel or system to an excessive amount of controlled pressure to observe its reaction. It can be performed on various pressurized vessels, including boilers, tubing, pipelines, and hydraulic hose systems. Technicians fill and pressurize the system beyond its maximum allowable working pressure (MAWP), typically 1.5 times the MAWP. The test stresses the system for 2 to 12 hours to monitor the structural integrity of its connections and materials.
Hydrostatic pressure testing is crucial for observing the expansion rate of a unit and system, determining if the system can handle the pressure it's rated for. It stress-tests the most important and weakest points of a hydraulic hose system, such as weld joints, fittings, flanges, and materials. If there are small or unobservable leaks, the pressure test can help identify them before they grow into more significant tears and ruptures.
For industrial applications like transporting fuel or chemicals, hydrostatic pressure testing is essential to guarantee the safety and integrity of the hydraulic hose system. Conducting hydrostatic pressure tests after initial commissioning ensures proper functioning of the vessels and hoses.